Piping Questions Related to Pipe and Fittings
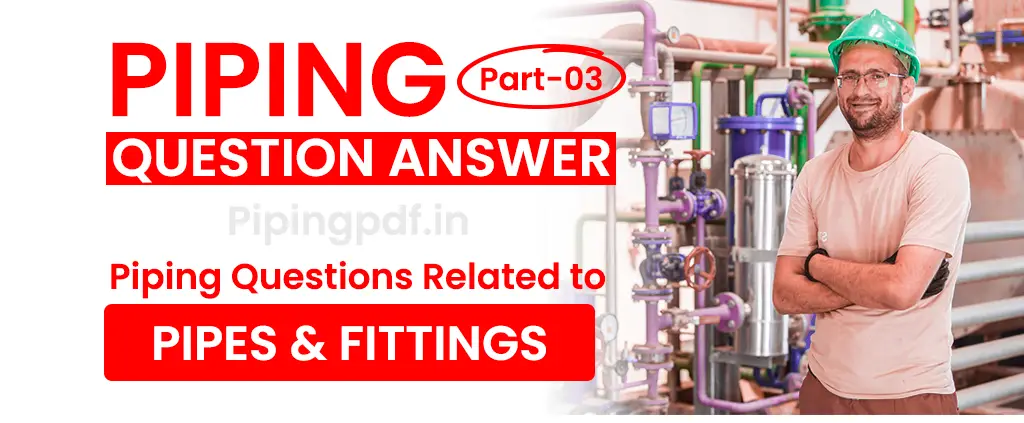
Q- How can flanges be classified based on Pipe Attachment?
Answer: – Flanges can be classified based on pipe attachment as
A) Slip – on. : – The Slip-on type flanges are attached by welding inside as well as outside. These flanges are of forged construction.
B) Socket Weld. : – The Socket Weld flanges are welded on one side only. These are used for small bore lines only.
C) Screwed. : – The Screwed-on flanges are used on pipe lines where welding cannot be carried out.
D) Lap Joint. : – The Lap Joint flanges are used with stub ends. The stub ends are welded with pipes & flanges are kept loose over the same.
E) Welding Neck. : – The Welding neck flanges are attached by butt welding to the pipe. These are used mainly for critical services where the weld joints need radiographic inspection.
F) Blind. : – The Blind flanges are used to close the ends which need to be reopened.
G) Reducing. : – The reducing flanges are used to connect between larger and smaller sizes without using a reducer. In case of reducing flanges, the thickness
of flange should be that of the higher diameter.
H) Integral. : – Integral flanges are those, which are cast along with the piping
component or equipment.
Q- How can flanges be classified based on Pressure- temperature ratings?
Answer: – Flanges are classified based on pressure temperature ratings as
A) 150 #
B) 300 #
C) 400 #
D) 600 #
E) 900 #
F) 1500 #
G) 2500#
Q- How can flanges be classified based on facing?
Answer: – Flanges are classified based on facing as
A) Flat face (FF)
B) Raised face (R/F)
C) Tongue and groove (T/G)
D) Male and female (M/F)
E) Ring type joint (RTJ)
Q- How can flanges be classified based on face finish?
Answer: – Flanges are classified based on face finish as
A) Smooth finish
B) Serrated finish
Q- Where the smooth finish flange & serrated finish flange finds its use?
Answer: – The smooth finish flange is provided when metallic gasket is used and serrated finish flange is provided when non-metallic gasket is used.
Q- What are the types of serrated finish provided on flange face?
Answer:
A) Concentric or
B) Spiral (Phonographic)
Q- How the serration on flanges is specified?
Ans: The serration on flanges is specified by the number, which is the Arithmetic Average Rough Height (AARH).
Q- Where the concentric serration is insisted for face finish?
Answer: Concentric serration are insisted for face finish where the fluid being carried has very low density and can find leakage path through cavity.
Q- How the Gaskets are classified based on the type of construction?
Answer: Based on the type of construction, gaskets are classified as
A) Full face.
B) Spiral wound metallic.
C) Ring type.
D) Metal jacketed.
E) Inside bolt circle.
Q- What is the most commonly used material for Gasket?
Answer: Compressed Asbestos Fiber
Q- Which type of gasket is recommended for high temperature & high-pressure application?
Answer: Spiral Wound Metallic Gasket.
Q- What are the criteria for selection of MOC of Spiral Wound metallic Gasket winding material?
Answer: The selection of material of construction for Gasket winding depends upon
A) The corrosive nature and concentration of fluid being carried.
B) The operating temperature of the fluid.
C) The relative cost of alternate winding material.
Q- What are the most common materials used for spiral wound metallic gasket winding?
Answer: The most commonly used material for spiral wound metallic gasket winding is
A) Austenitic stainless steel 304 with asbestos filler.
B) Austenitic stainless steel 316 with asbestos filler.
C) Austenitic stainless steel 321 with asbestos filler.
Q- Which material is used as filler material for spiral wound gasket in case of high temperature services?
Answer: For very high temperature services, graphite filler is used.
Q- What is centering ring in connection to spiral wound gasket?
Answer: Spiral wound gaskets are provided with carbon steel external ring called centering ring.
Q- What will be the AARH finish on flange face for using spiral wound gasket?
Answer: 125-250 AARH finish.
Q- On which type of flanges the use of spiral wound gasket are restricted?
Answer: In ASME B16.5 it does not recommend the use of 150# rating spiral wound gasket on flanges other than welding neck and lapped joint type.
Q- Up to what temperature limits the low-strength carbon steel bolts should not be used for flanged joints?
Answer: Flanged joints using low-strength carbon steel shall not be used above 200°C or below – 28°C
Q- How the pipe fittings are classified based on end connections?
Answer: Pipe fittings are classified based on end connection as
A) Socket weld fittings.
B) Screwed end fittings.
C) Beveled end or Butt weld fittings.
D) Spigot socket fittings.
E) Buttress end fittings.
Q- Up to what temperature the carbon steel materials shall be used?
Answer: Carbon steel materials shall be used for temperature up to 425°C
Q- Which material is used for temperature above 426°C?
Answer: Alloy steel materials shall be used for temperature above 426°C.
Q- Which type of material is used for corrosive fluid?
Answer: Stainless steel materials shall be used for corrosive fluid.
Q- Which type of piping materials are used for drinking water, instrument air, etc.?
Answer: Galvanized steel materials shall be used for drinking water, instrument air and NI lines (LP).
Q- What is the difference between Pipe and Tube?
Answer: Pipe is identified by NB and its thickness is defined by Schedule Number whereas Tube is identified by OD and its thickness as BWG (Birmingham wire gauge or 1/100 inch)
Q- From which size onward NB of the pipe is equal to the OD of the Pipe?
Answer: From the size 14” and onwards NB is equal to the OD of pipe.
Q- What should be the radius of long radius elbow?
Answer: 2D (Where “D” is the diameter of the pipe.)
Q- What should be the radius of short radius elbow?
Answer: 1D (Where “D” is the diameter of the pipe.)
Q- What is the basis of using of short radius & long radius elbow?
Answer: Long-radius elbows are used for small pressure drops whereas short-radius elbows are used for high-pressure drops, for catalyst flows long-radius elbows are used.
Q- Normally where do we use the following?
A. Eccentric reducers
B. Concentric reducers
Answer:
A) Eccentric reducers are used in Pump suction to avoid Cavitation and to maintain elevation (BOP) in the rack.
B) Concentric reducers are used in Pump discharge, and vertical pipeline, etc.
Q- Concentric reducer is used in pump suction. (Yes / No). Explain.
Answer: No. Air pockets may form if a concentric reducer is used at pump suction, which results in cavitation and cause damage to the Pump. To avoid this problem, Eccentric Reducer with a flat side up (FSU) is used in Pump Suction.
Q- Where the ERW spiral & longitudinal pipes are used?
Answer: Use depends upon the availability of pipes. There is nothing functional difference.
Q- Where the ERW & Seamless pipes are used?
Answer: – Above 18” ERW pipes are used and Below 18” seamless pipes are used. Seamless pipes can sustain higher temperature & pressure
Q- What is the main use of ASTM A53 & A106 Gr. B pipes?
Answer: ASTM A53 pipes are mainly used for utility services whereas A106 Gr. B pipes are used for high Pressure & high-temperature services.
Q- From which side of pipe will you take a branch connection?
Answer: Top Side – When fluid is Gas, Air or Steam and Cryogenic Service and
Bottom Side – When Fluid is Liquid
Q- Why don’t we take a branch for Cryogenic Service from bottom side though the fluid is in liquid state?
Answer: There is the chance of ice formation during normal operation and since ice flows from the bottom of the pipe it will block the branch pipe connection.
Q- Why do we provide High Point Vent (HPV) and Low Point Drain (LPD) in piping?
Answer:
HPV – For removing Air during Hydro-test.
LPD – For draining water after conducting Hydro-test.
Q- What do you mean by Jacketed Piping?
Answer: Jacketed piping is a type of piping that has an outer pipe surrounding an inner pipe. The annular space between the two pipes is filled with a heating or cooling medium. This type of piping is used to maintain the temperature of the process fluid flowing through the inner pipe.
Jacketed piping is commonly used in applications where the process fluid needs to be maintained at a specific temperature. Mostly used for molten Sulphur, Polymers service.
Q- What is the minimum distance to be maintained between two welds in a pipe?
Answer: The thumb rule is that the minimum distance between adjacent butt welds is 1D. If not, it is never closer than 1-1/2″. This is supposed to prevent the overlap of HAZs. The minimum spacing of circumferential welds between centerlines shall not be less than 4 times the pipe wall thickness or 25 mm whichever is greater.
Q- What do you mean by IBR and which lines come under IBR scope?
Answer: IBR Stands for Indian Boiler Regulation Act.
Steam lines with the conditions listed below come under the IBR scope
- Lines for which design pressure is 3.5 kg/sq. cm and above.
- Line size above 10” having design pressure 1.0 kg/sq. cm and above.
- Boiler feed water lines to steam generator, condensate lines to steam generator and flash drum
Q- What are Weldolet and Sockolet? And where they are used?
Answer: Weldolet and Sockolet are basically self-reinforced fittings.
Weldolet is used for Butt weld branch connection where standard tee is not available due to size restrictions and the piping is of critical / high-pressure service. And Sockolet is used for socket welding branch connection, which require reinforcing pad.
Q- What is the MOC for Superheated high pressure Steam Lines?
Answer: A 335 Gr. P 1 / P 11, Composition: Cr. – ½ Mo (P1) / 1¼ Cr. – ½ Mo (P11)
Q- What is the normal upstream and downstream straight length of orifice flow meter?
Answer: Upstream – 10D to 15D And Downstream – 5D
Piping Question Answer Series Part – 02
Download Piping Question Answer series Part – 03
Read Also
Download Free Piping PDF for Interview Preparation