Valves Introduction:
Valves: In the world of the oil & gas industry, valves play an important role in regulating the flow of various fluids within various networks of pipes and equipment. They are essential components that control the speed, pressure, and direction of fluids, ensuring the smooth and safe operation of refinery processes. This article will explore the different types of valves in pipelines & in oil and gas industry and their specific applications.
Type of Valves
Gate Valve
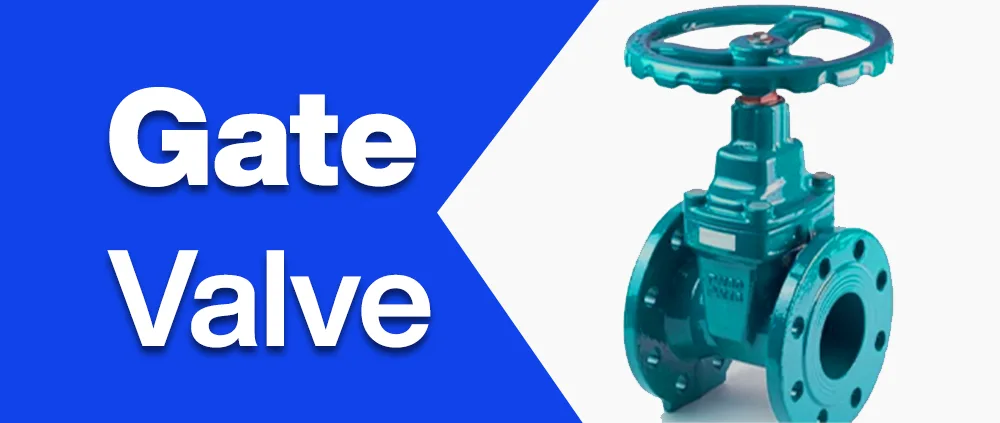
Gate valves are one of the most common types of valves found in refineries. Gate valves are typically used for isolation purposes in on-off applications. This valve has a gate-like mechanism that moves up and down to control fluid flow. When the valve is fully open, the gate is lifted, allowing unrestricted flow, and when fully closed, it forms a tight seal, preventing the passage of fluid. These valves are widely used for isolation purposes in crude oil and product pipelines as well as in oil and gas systems, water treatment plants, and general industrial applications
Globe Valve
Globe valves are designed with a globe-like structure and a movable disc that controls fluid flow. When the disc is lowered onto the seat, it restricts flow, and when raised, it allows fluid to pass through. Globe valves are commonly used in refining units that require precise control over flow rates and where throttling is necessary, such as in control loops, steam systems, and fractionation columns.
Usage: Globe valves are suitable for applications that require precise flow control and throttling. They provide good regulation capabilities due to the linear motion of their discs. Globe valves are commonly used in steam systems, cooling water systems and in applications where a controlled flow rate is essential.
Ball Valves
As the name suggests, ball valves consist of a ball-shaped closure element with a hole in its center. When the valve is open, the ball aligns with the pipeline, enabling fluid passage, and when closed, it rotates 90 degrees to block flow completely. Ball valves are popular in refineries because of their quick operation, tight shut-off capability, and suitability for high-pressure applications such as main-line pipelines and storage tanks.
Check Valve
Check valves, also known as non-return valves, allow fluid flow in only one direction, preventing backflow. They are critical in refinery systems to avoid the risk of process disruption, backflow contamination, and equipment damage. Check valves to find applications in pump discharge lines, cooling water systems, and gas and steam lines where unidirectional flow is essential.
Usage: Check valves are designed to allow fluid flow in one direction only and prevent backflow. They are important for preventing damage to equipment and pipelines due to reverse flow. Check valves are used in pump discharge lines, HVAC systems, and various water distribution systems.
Butterfly Valves
Butterfly valves consist of a circular disc positioned within the pipeline that rotates to regulate fluid flow. When the disc is parallel to the pipe, it allows unrestricted flow, and when it is perpendicular, it obstructs the flow. These valves are commonly used in larger diameter pipes for bulk fluid handling, such as in crude oil transfer lines and cooling water systems.
Usage: Butterfly valves are used in applications that require large flow capacities and low-pressure drops. They provide a simple and cost-effective solution for regulating flow. Butterfly valves are commonly found in water and wastewater treatment, ventilation systems, and cooling water systems.
Control Valves
A control valve is a valve used to control the flow of fluid in a process. They are used in a wide variety of industries including the oil and gas industry. In the oil and gas industry, control valves are used to control the flow of oil, gas, and other fluids in pipelines, wells, and processing plants.
Control valves are an essential part of the oil and gas industry. They help ensure that the flow of fluids is controlled and that processes operate safely and efficiently.
Classification
Control valves are generally classified according to the type of closure member they use. The most common types of closure members for control valves are:
Ball Valve, Globe Valve, Butterfly Valve, Plug Valve
Control valves can also be classified according to the type of actuator they use. The most common types of actuators for control valves are:
Electric actuators: Electric actuators use an electric motor to open and close a valve.
Pneumatic Actuators: Pneumatic actuators use compressed air to open and close valves.
Hydraulic Actuators: Hydraulic actuators use hydraulic fluid to open and close valves.
The type of control valve used in the oil and gas industry depends on the specific application. For example, ball valves are often used in pipelines because they are able to withstand high pressures and temperatures. Butterfly valves are often used in wells because they are able to tightly seal the wellbore.
PSV (Pressure Safety Valve)
A pressure safety valve, also known as a pressure relief valve (PRV), is a type of valve designed to automatically release excess pressure from a system or equipment to prevent overpressure conditions. When the pressure inside the system exceeds a predetermined set point, the PSV opens to discharge the excess pressure, and when the pressure returns to the normal operating range, the valve closes. PSVs are used to protect various industrial equipment, pipelines, and vessels from damage caused by overpressure, thereby ensuring the safety of the overall system.
Diaphragm Valves
Diaphragm valves are ideal for handling corrosive and abrasive fluids. They have a flexible diaphragm as the closing element, which separates the fluid from the valve body. Diaphragm valves are used in pharmaceuticals, chemical processing and water treatment plants.
Needle Valve
Needle valves are used for precise flow control in low-flow applications. They have a slender, pointed stem that provides fine adjustment to the flow rate. Needle valves are commonly used in instrumentation systems, gauge isolation, and flow metering applications.
Plug valve
The plug valve has a cylindrical or conical plug as the closing element. They offer a simple design and are suitable for on-off and flow control applications. Plug valves are commonly used in fuel and oil systems, water treatment, and gas distribution.
Solenoid Valve
Solenoid valves are electro-mechanically operated valves used for rapid and automatic flow control. They find applications in automation systems, irrigation and various industrial processes.
Conclusion
In refineries, valves are that components which regulate and control the flow of fluids, ensuring the safe and efficient operation of these massive industrial complexes. Each valve type plays a unique role in the refining process, from enabling precise flow control to ensuring the protection of equipment and personnel.
The proper selection, installation, and maintenance of valves are crucial for optimizing refinery operations, enhancing safety, and minimizing downtime.
Read and Download more latest free PDF
Also Read What is Piping