Introduction of Nuts and Bolts
In all industries, nuts, and bolts are the main components that hold together the machinery and structures that run our world. These nuts and bolts play an important role in ensuring the integrity and security of a variety of applications, from industrial equipment to critical infrastructure.
In the oil and gas industry safety, reliability, and efficiency are of paramount importance. These industries rely heavily on pipelines, equipment, and infrastructure to transport, store, and process hydrocarbons.
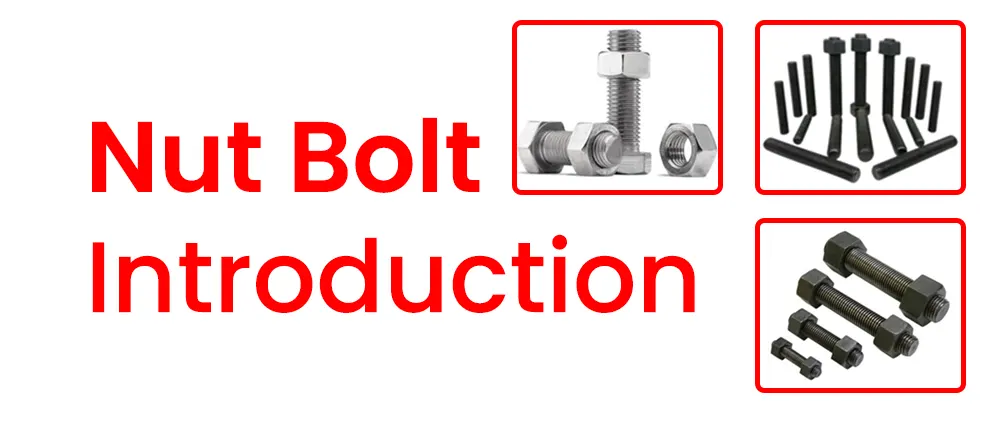
The integrity of these systems is ensured, in part, by using high-quality components that adhere to strict codes and standards. Among these components, nuts and bolts play a crucial role in maintaining structural integrity, leak prevention, and overall operational safety.
In this article, we will discuss significance of nuts and bolts in the oil and gas industry and the specifications of nuts and bolts, especially focusing on the well-known ASTM A193 B7 and its related nut specification ASTM A194 2H, to understand their importance and applications.
The Importance of Nuts and Bolts in Oil and Gas Applications
In the oil and gas industry, nuts and bolts are utilized for joining various components, including pipes, flanges, valves, and other equipment, forming a network that carries and processes hydrocarbons. These connections must be able to withstand high pressures, extreme temperatures, and other harsh conditions that are characteristic of oil and gas operations. Nut bolts provide the necessary strength and reliability to ensure the overall safety and efficiency of the infrastructure.
ASME B31.3 Code – An Overview
The ASME B31.3 code, titled “Process Piping”, is a widely recognized standard for the design, construction, inspection, and maintenance of process piping systems. The code is developed and maintained by the American Society of Mechanical Engineers (ASME) and is widely adopted in the oil and gas industry. It provides guidelines for the materials, design, installation, testing, testing and operation of piping systems.
Adherence to ASME B31.3 is essential for oil and gas companies to ensure the integrity and safety of their piping systems. The code covers a wide range of topics, including material selection, design factors, pressure and temperature limits, welding procedures, and the use of fasteners including nuts and bolts.
Choosing the Right Nuts and Bolts
When it comes to selecting nuts and bolts for oil and gas applications, strict adherence to the ASME B31.3 code is critical. The code specifies various requirements for the material, dimensions, and performance of fasteners used in process piping systems.
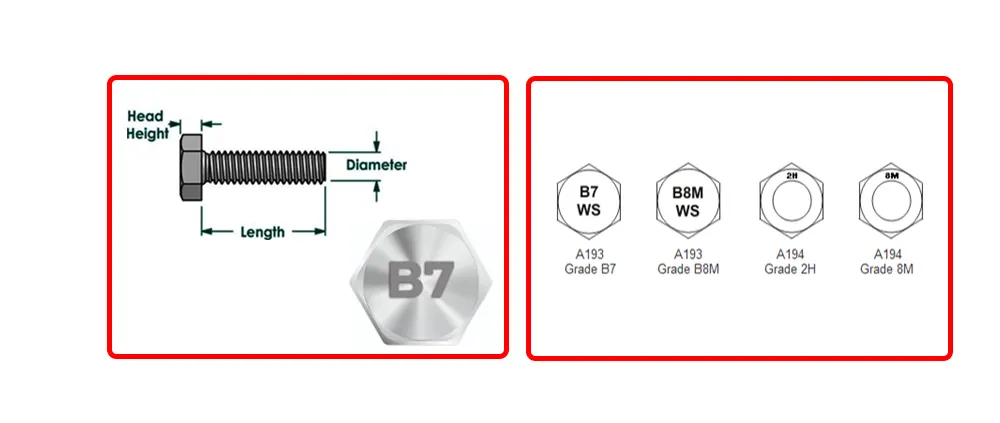
Materials
The ASME B31.3 code mandates the use of appropriate materials for nuts and bolts based on operating conditions, such as pressure, temperature, and the media being transported. Common materials include carbon steel, alloy steel and stainless steel, each with specific properties suitable for different environments.
Dimensions
The code outlines detailed dimensions for nut bolts, including thread specification, nut type (hex, heavy hex, etc.), and bolt size, to ensure proper fit and compatibility with accompanying flanges, valves, and equipment.
Performance
Nuts and bolts must meet specific performance criteria including tensile strength, yield strength, elongation and hardness. These mechanical properties ensure that the fastener can handle the loads and stresses encountered during operation.
Installation and inspection
Proper installation of nut bolts is critical to guaranteeing the integrity of the piping system. The ASME B31.3 code provides guidelines for torque values, bolt tightening procedures, and the use of lubricants during installation to achieve proper preload and prevent fasteners from over- or under-tightening.
Additionally, regular inspection and maintenance is necessary to identify any signs of corrosion, wear or deterioration of the nut bolt. This is important to prevent potential leaks, failures or accidents that could lead to environmental hazards, production interruptions or personnel harm.
ASTM A193 B7 Specification
ASTM A193 is a widely recognized specification covering alloy steel and stainless steel bolting materials for high temperature or high pressure service. Among the various grades, B7 is one of the most commonly used grades due to its exceptional strength, heat resistance and suitability for a wide range of applications.
Composition and Properties of Nuts and Bolts
ASTM A193 B7 bolts are made from medium-carbon alloy steel, typically AISI 4140, which undergoes heat treatment to achieve the desired mechanical properties. This treatment includes quenching and tempering to increase the strength and hardness of the material. B7 bolts exhibit excellent tensile strength, yield strength and toughness, making them ideal for applications subject to high stresses and elevated temperatures.
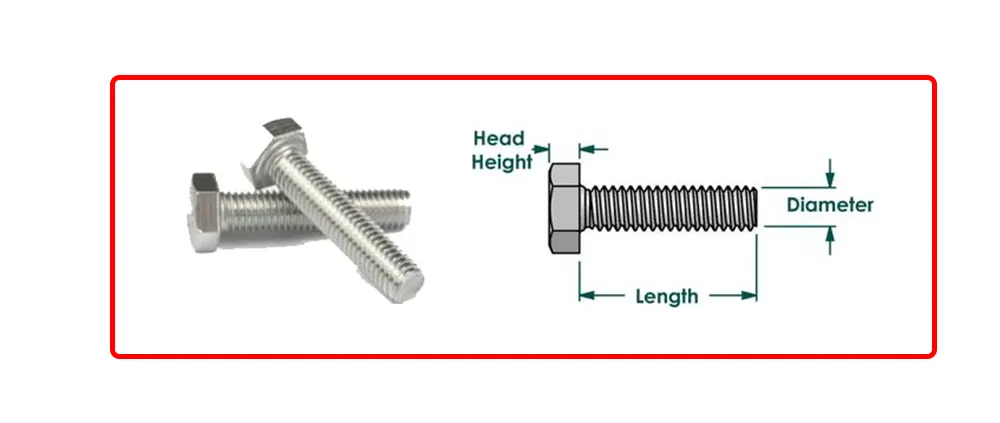
Applications of Bolts
ASTM A193 B7 Bolts are widely used in industries such as oil and gas, petrochemical, power generation and construction. They are typically employed in flanged connections, pressure vessels, valves, and pipelines, where their superior mechanical properties and corrosion resistance are essential to ensure long-term performance and safety.
ASTM A194 2H Specification
ASTM A194 is the specification that covers a range of nuts for use with various bolting materials including carbon steel, alloy steel and stainless steel. ASTM A194 2H is specifically designed to be used in conjunction with ASTM A193 B7 bolts, creating a strong and reliable fastening system.
Structure and Properties
ASTM A194 2H nuts are manufactured from carbon steel and undergo the same quenching and tempering process as ASTM A193 B7 bolts. This treatment provides increased hardness and tensile strength to the nuts, allowing compatibility with the high-strength properties of B7 bolts.
Applications of Nuts
ASTM A194 2H nuts are primarily used in conjunction with ASTM A193 B7 bolts in critical applications that demand exceptional strength and resistance to extreme conditions. These nuts are commonly found in pressure vessels, heat exchangers, flanged connections and other equipment where reliable fastening is essential to ensure operational safety and prevent leaks.
Benefits of using ASTM A193 B7 and ASTM A194 2H Nuts and Bolts
Enhanced Strength
The combination of the ASTM A193 B7 bolts and ASTM A194 2H nuts provides superior strength and durability, providing a secure and reliable fastening solution for critical applications.
High Temperature Resistance
Both B7 bolts and 2H nuts are designed to withstand elevated temperatures, making them suitable for use in high-temperature environments such as power plants and steam pipelines.
Corrosion Resistance
The alloy steel construction of the B7 bolts and the quenched and tempered carbon steel of the 2H nuts provide excellent corrosion resistance, ensuring long service life even in corrosive environments.
Difference between Stud Bolts and Machine Bolts
Stud bolts and machine bolts are both types of fasteners used in different applications, but they have some key differences in design and use. Here are the main differences between stud bolts and machine bolts:
Design & Size
Stud Bolt
A stud bolt is a threaded rod with threads on both ends. It usually has a non-threaded part in the middle, known as the shank. Shank length is selected based on the specific application and the required clamping force.
Machine Bolt
A machine bolt is a fastener with a shank that is fully threaded from head to end. It does not have a non-threaded part like a stud bolt. The entire length of the machine bolt is threaded.
Objective
Stud Bolt
Stud bolts are often used in situations where components need to be assembled on either side of a structure, with the stud acting as a bridge between them. The unthreaded shank allows for more precise tension and positioning of components, making it suitable for applications such as flange connections in pipelines and other large structures.
Machine Bolt
Machine bolts are commonly used in situations where two or more parts need to be held together with a secure fastening. They are widely used in machinery, equipment and general construction where a strong, threaded fastener is required.
Establishment
Stud Bolt
Installing a stud bolt involves threading one end into a component, then putting a nut on the other threaded end to secure the other component. Stud bolts can be easily tightened at both ends using two wrenches, making assembly and disassembly more convenient.
Machine Bolt
Machine bolts are installed by threading directly into a pre-tapped hole or nut. They usually require access to both ends to tighten or loosen them, which can be more cumbersome in some applications than stud bolts.
Stud bolt and Machine bolt
Stud Bolt
Stud bolts require nuts on both ends to secure the components. The nut can be easily torqued to obtain the desired clamping force.
Machine Bolt
A machine bolt requires a nut on only one end, as the other end is already threaded into the component or material to be fastened.
Conclusion
Nuts and bolts may seem like small components, but their role in ensuring the stability and safety of various structures and machinery cannot be underestimated. When it comes to demanding applications that require exceptional strength, temperature resistance, and corrosion protection, the combination of the ASTM A193 B7 bolt and ASTM A194 2H nut proves to be an excellent choice. These specifications set high standards for quality and reliability, making them indispensable in critical industries such as oil and gas, petrochemical and power generation, where safety and performance are of the utmost importance.
Read More Also
Piping Interview question answer free PDF
What is Piping Used in oil and gas Industry
What are flanges and their types used in Piping
What are Valves and their types used in piping
4 thoughts on “Types of Nuts and Bolts pdf used in the oil and gas industry”