Introduction of Distillation Column
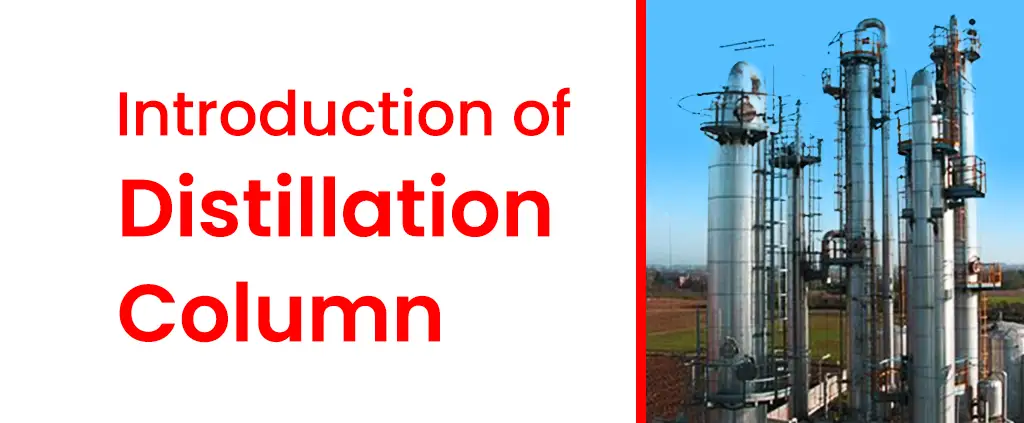
In the world of petroleum refineries, distillation columns is an essential item for the primary separation of crude oil into various valuable products which is used to distillate the liquid mixtures into its component parts, or fractions, based on the differences in volatilities. These massive structures are integral to the refining process, which enables raw crude oil to be transformed into a range of essential fuels and petrochemicals that power our modern society. This article throws light upon the importance of distillation columns in refineries and explores the different types employed in the pursuit of refining excellence.
Importance of Distillation Columns in Refineries
Crude oil is a complex mixture of hydrocarbons, consisting of different compounds with different boiling points. Distillation processes in refineries use these different boiling points to separate crude oil into distinct fractions with specific applications. This is important because a variety of products such as gasoline, diesel, jet fuel and petrochemical feedstock require precise compositions to meet stringent quality and performance standards.
Distillation columns are tasked with handling this separation, acting as tall vertical vessels that enable the fractionation of crude oil through a process called fractional distillation. These columns play an important role in refining as they form the foundation for all subsequent refining steps including cracking, reforming, alkylation and isomerization.
Types of Distillation Columns in Refineries
Atmospheric Distillation Column
The atmospheric distillation column is the primary unit in any refinery, handling the initial separation of crude oil into several major fractions.
It operates at atmospheric pressure, with the feedstock entering the column near its base and vaporizing as it ascends.
The fractions are collected at different heights within the column based on their boiling points, with the highest temperature at the bottom and the lowest temperature at the top.
Typical fractions include gases (for example, LPG), naphtha, kerosene, diesel, and atmospheric residues.
Vacuum Distillation Column
The vacuum distillation column operates at low pressure, allowing the separation of high-boiling fractions that cannot be effectively separated in an atmospheric column.
The column can handle heavy hydrocarbons, such as vacuum gas oil and vacuum residue, which are essential for lubricants and other heavy fuel products.
Fractionating Column
Fractionating columns are specialized distillation units used to further refine specific fractions obtained from atmospheric or vacuum distillation.
These columns can separate the initial fractions into more narrow cuts, ensuring that the desired product quality is achieved.
Side Stripper Column
Side stripper columns are used to remove lighter components from heavier fractions to meet product specifications.
They help in obtaining a purer and more valuable product by removing impurities or undesirable components.
Distillation Columns can also be categories as
Batch Columns
The feed to the column is introduced batch-by-batch in a batch procedure. In other words, the distillation process is carried out once the column is charged with a “batch” of material. A new batch of feed is supplied once the intended task has been completed.
Continuous Columns
Continuous columns, on the other hand, handle a continuous feed stream. Unless there is a problem with the column or nearby process units, there are no interruptions. They are the more prevalent of the two varieties and are able to handle high throughputs. We will solely focus on this category of columns.
Main components of distillation columns
Distillation columns are made up of several components, each of which is used to either transfer heat energy or enhance material transfer.
A typical distillation column consists of several major components.
a) Vertical Shell
A vertical casing or shell where the separation of liquid components is carried out.
b) Column internals
Column Internals such as trays/plates and/or packings that are used to enhance component separation.
c) Reboiler
A Reboiler used to provide the evaporation needed for the distillation process
d) Condenser
A Condenser is used to cool and condense the vapors leaving the top of the column
e) Reflux drum
A reflux drum is used to capture the condensed vapor from the top of the column so that the liquid (reflux) can be recycled back into the column.
Basic Operations and Terminology
The liquid mixture to be processed is known as the feed and it is usually poured into a tray somewhere in the middle of the column known as the feed tray. The feed tray divides the column into a top (enriching or reforming) section and a bottom (stripping) section. The feed flows down the column where it is collected at the bottom in the reboiler.
Heat is supplied to the reboiler to generate steam. The source of heat input can be any suitable fluid, although in most chemical plants it is usually steam. In refineries, the heat source may be the output stream of other columns. The steam raised in the reboiler is re-injected into the unit at the bottom of the column. The liquid removed from the reboiler is known as the bottoms product or simply bottoms.
The vapor moves upward in the column, and as it exits the top of the unit, it is cooled by a condenser. The condensed liquid is collected in a holding vessel known as a reflux drum. Some of this liquid is recycled back to the top of the column and is called reflux. The condensed liquid removed from the system is known as the distillate or top product.
Conclusion
In conclusion, distillation columns are the backbone of petroleum refineries, where the separation of crude oil into essential products occurred. From atmospheric and vacuum distillation columns to specialized fractionation and side stripper columns, each type makes a specific contribution to the complexity and efficiency of the refining process. As technology continues to advance, these critical units will evolve, enabling refineries to meet the growing demand for cleaner and more diverse petroleum products.