(NDT) Non-Destructive Testing is a fundamental process in numerous industries that ensures the quality, reliability, and safety of materials without causing any damage. As a suite of inspection techniques, NDT plays a critical role in identifying defects in components, infrastructure, and systems. From the aerospace sector to manufacturing, NDT helps in maintaining safety standards, improving product quality, and reducing costs.
In this detailed guide, we will explore Non-Destructive Testing (NDT) methods, their various applications, the benefits they provide, and discuss future trends in this essential field.
Understanding Non-Destructive Testing (NDT)
Non-Destructive Testing (NDT) refers to the collection of techniques used to evaluate the properties of a material, component, or structure without causing any damage to it. Unlike destructive testing, NDT allows materials to remain in service while still being examined for defects such as cracks, corrosion, and other irregularities.
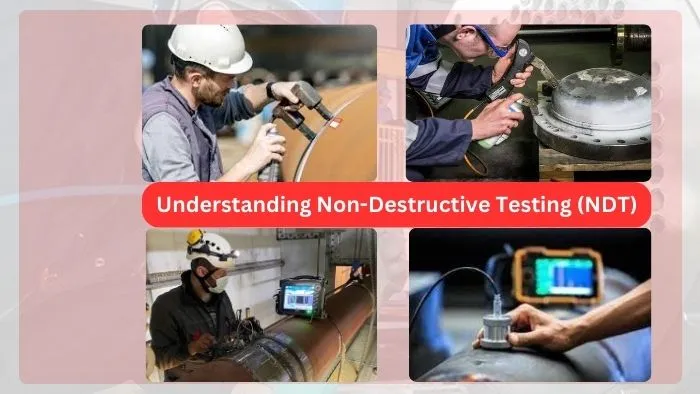
NDT is particularly useful in industries where the reliability and safety of components are paramount, including:
- Aerospace
- Oil and Gas
- Automotive
- Construction
- Power Generation
By applying these techniques, industries can detect flaws early in a product’s life cycle, preventing potential failures that could result in financial loss, environmental damage, or even loss of life.
The Importance of NDT in Safety and Compliance
One of the primary reasons NDT is indispensable in many industries is that it ensures compliance with safety regulations. For instance, in the oil and gas sector, pipelines, storage tanks, and other critical infrastructure are frequently inspected using NDT to detect corrosion or cracks. Similarly, in aerospace, the failure of a single component could have catastrophic consequences, making regular NDT inspections mandatory.
Moreover, NDT aids in product quality control by identifying defects before materials or components are incorporated into final products. By doing so, manufacturers avoid costly recalls or product failures. In regulated industries, such as nuclear energy, regular NDT inspections are required to meet both international standards and regulatory frameworks.
Popular Methods of Non-Destructive Testing
There are various NDT methods, each suited for different types of materials, defect types, and applications. Here is an in-depth look at the most commonly used NDT methods:
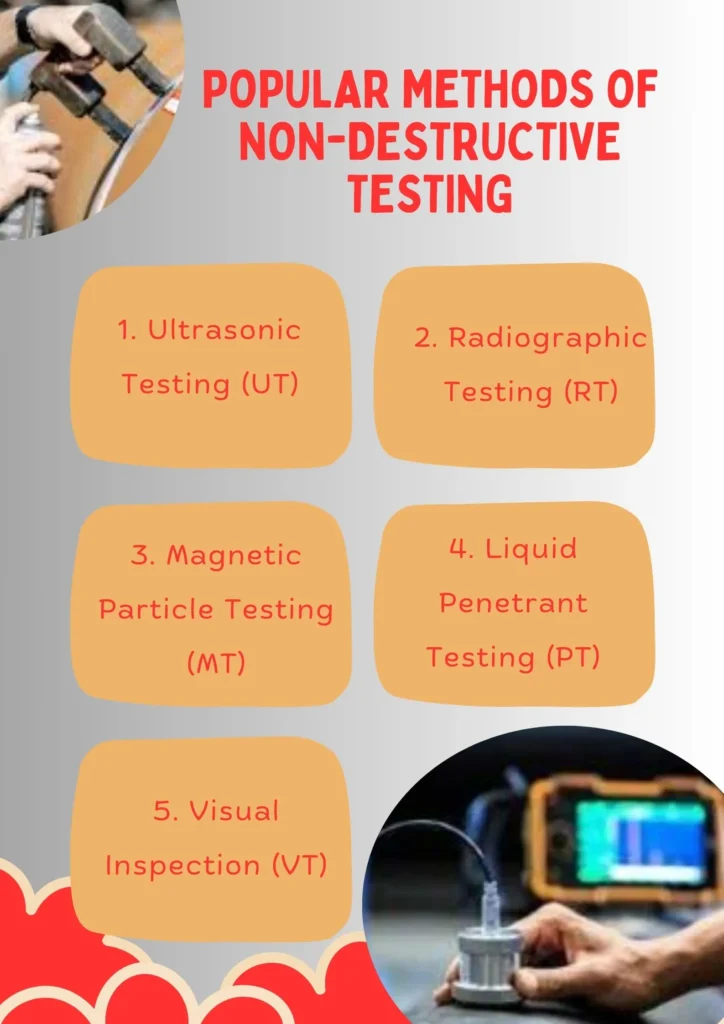
1. Ultrasonic Testing (UT)
Ultrasonic Testing (UT) is a highly sensitive method that uses high-frequency sound waves to detect defects within a material. A transducer emits ultrasonic waves that travel through the material, and any reflection of these waves from a flaw or defect is detected and analyzed.
- Applications: UT is widely used in the aerospace industry to inspect aircraft components and in oil and gas pipelines to detect internal corrosion.
- Example: In the automotive industry, ultrasonic testing is used to ensure that critical components such as engine blocks and transmission cases are free from internal flaws, enhancing vehicle safety and performance.
- Advantages:
- Can detect both surface and subsurface defects.
- Can measure material thickness.
- Non-invasive and fast.
2. Radiographic Testing (RT)
Radiographic Testing (RT) uses X-rays or gamma rays to penetrate materials and capture images of their internal structures. This method is extremely effective in detecting internal defects that are not visible from the outside.
- Applications: RT is commonly used in industries like nuclear energy to examine welds, and in automotive for the inspection of castings.
- Example: In the oil and gas industry, radiographic testing is applied to inspect the integrity of welds in pipelines. Detecting cracks, corrosion, or inclusions in the welds early can prevent catastrophic failures.
- Advantages:
- Can detect internal defects.
- Permanent records of inspection (in the form of images).
- Can be used on a variety of materials, including metals, plastics, and composites.
3. Magnetic Particle Testing (MT)
Magnetic Particle Testing (MT) is used primarily for inspecting ferromagnetic materials. A magnetic field is applied to the material, and magnetic particles are introduced. If there are surface or near-surface flaws, the magnetic particles will be attracted to these regions, revealing the defect.
- Applications: MT is widely used in the construction industry for inspecting steel structures and welds.
- Example: In the railway industry, magnetic particle testing is used to inspect the wheels and axles of trains, ensuring that surface cracks are detected before they lead to failures in service.
- Advantages:
- Simple, quick, and cost-effective.
- Effective for surface and near-surface flaws.
- Provides immediate results.
4. Liquid Penetrant Testing (PT)
Liquid Penetrant Testing (PT) involves applying a liquid (dye or fluorescent) to the surface of a material. The liquid seeps into surface defects, and excess liquid is removed. A developer is then applied, which draws the penetrant out of the defect, making it visible under a special light.
- Applications: PT is used in metal fabrication to inspect the surface quality of components.
- Example: In the aerospace sector, liquid penetrant testing is applied to detect surface cracks in turbine blades, preventing potential failures during flight operations.
- Advantages:
- Low cost and simple to perform.
- Effective for detecting small surface-breaking defects.
- Can be applied to a wide range of materials, including non-metallic.
5. Eddy Current Testing (ET)
Eddy Current Testing (ET) is used to detect surface and near-surface defects in conductive materials. A coil carrying an alternating current is placed near the surface of the material, creating eddy currents. Defects disrupt these currents, allowing inspectors to identify flaws.
- Applications: ET is widely used in the aerospace industry, especially for inspecting aircraft fuselages and landing gears.
- Example: In the nuclear industry, eddy current testing is employed to inspect heat exchanger tubes in nuclear power plants, identifying any flaws that could compromise the system’s efficiency.
- Advantages:
- Can detect very small cracks and corrosion.
- Can be used on coated materials.
- Fast and provides immediate results.
6. Visual Inspection (VT)
Visual Inspection (VT) is one of the oldest and simplest NDT methods. It involves a trained inspector visually examining the material or structure for defects. This method is often enhanced by the use of magnifying glasses, borescopes, or cameras.
- Applications: VT is often used in combination with other NDT methods, especially in construction and manufacturing.
- Example: In the construction industry, visual inspection is commonly used to assess the surface condition of steel components before they are incorporated into large structures such as bridges or skyscrapers.
- Advantages:
- Low cost and widely accessible.
- Immediate results.
- Ideal for surface defects.
Detailed Applications of Non-Destructive Testing
Non-Destructive Testing (NDT) is used across multiple industries to ensure safety, compliance, and efficiency. Each industry employs different NDT methods based on the materials, components, and types of defects that need to be identified. Below are some industry-specific applications of NDT.
1. Aerospace Industry
In the aerospace sector, the importance of NDT cannot be overstated. Aircraft components are subjected to extreme conditions, including high pressure, temperature variations, and mechanical stress. Therefore, ensuring the structural integrity of components is critical.
- Methods Used: Ultrasonic Testing (UT), Radiographic Testing (RT), and Eddy Current Testing (ET).
- Example: During routine maintenance, an airline may use ultrasonic testing to inspect the fuselage for hidden cracks or fatigue that could compromise safety during flight.
2. Oil and Gas Industry
The oil and gas industry is known for its harsh operating environments, where equipment such as pipelines, storage tanks, and drilling platforms are subjected to extreme conditions. NDT is employed to prevent leaks, spills, and other potentially catastrophic failures.
- Methods Used: Magnetic Particle Testing (MT), Radiographic Testing (RT), and Ultrasonic Testing (UT).
- Example: In offshore oil rigs, ultrasonic testing is used to monitor the integrity of high-pressure pipelines to ensure they remain safe under extreme conditions.
3. Manufacturing Industry
In manufacturing, NDT is essential to ensure product quality, prevent defects from reaching the end consumer, and reduce waste. Whether it’s metal casting, plastic molding, or automotive parts, NDT ensures that products meet rigorous quality standards.
- Methods Used: Liquid Penetrant Testing (PT), Visual Inspection (VT), and Ultrasonic Testing (UT).
- Example: In the automotive sector, liquid penetrant testing is used to detect surface cracks in engine blocks, ensuring that only defect-free components make it into vehicles.
4. Construction Industry
Safety is paramount in construction, as the failure of a structural component could lead to catastrophic outcomes. NDT ensures that materials such as steel, concrete, and composites used in bridges, buildings, and other structures are free from defects.
- Methods Used: Visual Inspection (VT), Magnetic Particle Testing (MT), and Ultrasonic Testing (UT).
- Example: NDT is used extensively during the construction of high-rise buildings to inspect the welds in steel structures, ensuring they meet safety standards.
5. Power Generation Industry
In the power generation industry, components like turbines, boilers, and pressure vessels are subjected to high temperatures and pressures. NDT plays a critical role in maintaining these systems’ reliability and safety.
- Methods Used: Radiographic Testing (RT), Ultrasonic Testing (UT), and Eddy Current Testing (ET).
- Example: In nuclear power plants, eddy current testing is used to inspect steam generator tubes for defects that could lead to reactor shutdowns.
Benefits of Non-Destructive Testing
Non-Destructive Testing offers several benefits, making it an indispensable tool in quality control and safety assurance across industries. Here are some of the key advantages:
1. Reduces Maintenance Costs
By identifying potential problems early, NDT allows for preventative maintenance, reducing the likelihood of costly repairs or replacements. This is especially beneficial in industries such as oil and gas and aerospace, where equipment failure can lead to significant financial losses.
2. Enhances Safety
NDT ensures that critical components and structures are safe for use, preventing accidents, injuries, and fatalities. Industries like nuclear energy rely on regular NDT inspections to ensure the safe operation of their facilities.
3. Minimizes Downtime
NDT can be performed while components are still in service, reducing the need for lengthy shutdowns. For example, ultrasonic testing of pipelines in a refinery can be done without interrupting production, saving time and costs.
4. Improves Product Quality
By detecting defects before they lead to failures, NDT ensures that products meet the required standards. In automotive manufacturing, for instance, NDT helps maintain high-quality control, ensuring that vehicles are safe and reliable.
Emerging Trends in Non-Destructive Testing
With advancements in technology, NDT methods continue to evolve, making inspections more efficient and accurate. Here are some key trends shaping the future of NDT:
1. Automated and Robotic NDT
Automation is making NDT inspections faster and more reliable. Robots equipped with NDT technologies can perform inspections in hazardous or hard-to-reach areas, improving safety and reducing human error.
- Example: In the oil and gas industry, robotic crawlers equipped with ultrasonic sensors are used to inspect pipelines and storage tanks, reducing the need for human inspectors in dangerous environments.
2. Artificial Intelligence (AI) and Machine Learning
AI and machine learning are being integrated into NDT to improve data analysis and defect detection. These technologies can process large amounts of data quickly and accurately, allowing for more precise assessments.
- Example: In the aerospace industry, AI-driven systems are used to analyze ultrasonic data from aircraft fuselage inspections, reducing the time required for analysis and improving the accuracy of defect detection.
3. Remote NDT
With the rise of the Industrial Internet of Things (IIoT), NDT systems can now be connected to remote monitoring platforms. This allows real-time inspection data to be transmitted and analyzed from anywhere in the world, improving efficiency and reducing the need for on-site inspections.
- Example: In nuclear power plants, remote NDT systems are used to monitor critical components continuously, allowing operators to identify potential issues before they become critical.
Conclusion
Non-Destructive Testing (NDT) is an essential tool for ensuring the quality, safety, and reliability of materials and components in various industries. From aerospace to oil and gas, NDT methods such as Ultrasonic Testing, Radiographic Testing, and Magnetic Particle Testing are used to detect defects and prevent failures.
The future of NDT looks promising, with advancements in automation, artificial intelligence, and remote technologies shaping the next generation of testing methods. By investing in the right NDT solutions, industries can reduce maintenance costs, improve product quality, and ensure the safety of their operations.
Read Also
Download Free Piping PDF for Interview Preparation
Download Free Piping PDF for Interview Preparation
What is gasket and their types
What is a valve and its types? Â