Introduction to High Pressure Valves
High Pressure Valves
High pressure valves are a crucial component in various industries, particularly where systems must handle extreme pressure levels. These valves are designed to withstand high pressure while controlling the flow of liquids or gases. In sectors like oil and gas, chemical processing, and power generation, the need for high pressure valves is indispensable (Indispensable means absolutely necessary; cannot be done without. It implies that something is essential or crucial for a particular task or situation.) due to the nature of the operations involved.
These valves play a vital role in ensuring safety, optimizing performance, and maintaining operational efficiency. In this article, let’s take a look at high-pressure valves, exploring their types, functions, applications, and the benefits they offer in high-demand environments.
Types of High Pressure Valves
Understanding the different types of high pressure valves is critical for selecting the right one for your specific application. Here are the most common types:
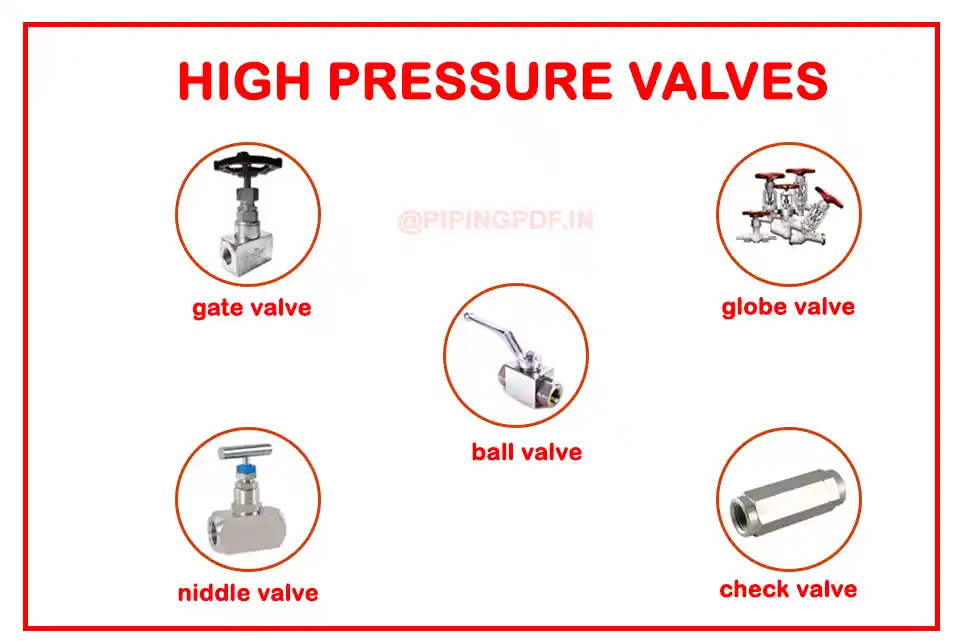
1. Ball Valves
Ball valves are designed with a spherical disc that controls the flow of liquids and gases. When the valve is open, the ball’s hole aligns with the flow, allowing materials to pass through. When closed, the hole is perpendicular to the flow, effectively stopping it. Ball valves are favored for high-pressure systems because of their durability and ability to handle high flow rates.
2. Gate Valves
Gate valves operate by lifting a gate to allow the flow of liquid or gas through a pipeline. When fully open, gate valves provide minimal flow resistance, making them ideal for applications requiring full, unobstructed flow. Their ability to function under high pressure makes them a common choice in the oil and gas industries.
3. Globe Valves
Globe valves are used to regulate flow in a pipeline. These valves are designed with a disc that moves perpendicular to the flow path, providing a throttling effect (Reducing fluid pressure by passing it through a narrow opening). Globe valves are preferred when precise flow control is necessary in high-pressure applications.
4. Needle Valves
Needle valves are known for their precision (exactness or accuracy) in controlling flow. These valves are equipped with a slender, needle-like plunger, which fits into the seat tightly, making them suitable for delicate adjustments. In high-pressure environments, needle valves ensure fine-tuned control of flow rates.
5. Check Valves
Check valves are designed to prevent backflow in a system. They operate automatically, only allowing flow in one direction, which is critical in preventing damage caused by reverse flow in high-pressure systems. Their automatic nature makes them a low-maintenance option in many industries.
Key Applications of High Pressure Valves
High-pressure valves are essential across various industries, particularly where systems must endure extreme pressures. Below are some of the key areas where these valves are commonly utilized:
1. Oil and Gas Industry
In the oil and gas sector, high pressure valves play a pivotal role in exploration, production, and transportation. These valves help manage the flow of oil and gas through pipelines, ensuring safe and efficient transportation. In refineries, high-pressure valves regulate the movement of fluids during complex processes, maintaining operational safety.
2. Chemical Processing
In chemical plants, controlling the flow of hazardous liquids and gases at high pressure is critical to maintaining safety and process efficiency. Globe valves and needle valves are commonly used in these environments for their precise flow control capabilities. These valves can handle the corrosive nature of many chemicals while ensuring that the systems operate within safe pressure limits.
3. Power Generation
Power plants, particularly those involving steam and hydraulic systems, rely heavily on high pressure valves to regulate the flow of water, steam, and gas under intense pressures. In nuclear and conventional power plants, valves must endure extreme temperatures and pressures while maintaining a secure flow of fluids.
4. Aerospace and Defense
The aerospace and defense industries require components that can withstand extreme pressure and temperature conditions. High pressure valves are used in fuel systems, hydraulics, and air supply systems for aircraft and defense vehicles, ensuring performance reliability under critical conditions.
5. Water and Wastewater Treatment
In the water and wastewater treatment sectors, high pressure valves control the flow and pressure of fluids in large treatment plants. These valves must endure continuous use in environments that demand both precision and durability, especially in handling treated water under pressure.
Benefits of High Pressure Valves
1. Enhanced Safety
One of the most significant advantages of high pressure valves is their ability to enhance safety in systems dealing with extreme pressures. By providing reliable flow control, these valves reduce the risk of equipment failure and hazardous accidents. Properly functioning valves prevent leaks and ruptures, safeguarding both the system and personnel.
2. Improved Efficiency
Valves designed for high-pressure systems contribute to overall operational efficiency. By ensuring the controlled and precise movement of fluids, they help optimize the performance of pumps, compressors, and other equipment. This efficiency reduces energy consumption and increases the lifespan of industrial machinery.
3. Durability and Longevity
High pressure valves are built to endure the most demanding conditions. Their materials, typically stainless steel or other high-grade alloys, ensure resistance to wear, corrosion, and extreme temperatures. This durability translates into fewer maintenance requirements and a longer operational lifespan.
4. Versatility
The versatility of high pressure valves lies in their ability to function across a wide range of industries and applications. From oil refineries to aerospace systems, these valves are designed to meet the unique demands of various environments, ensuring fluid management remains seamless and safe.
Key Considerations for Choosing High-Pressure Valves
When selecting high pressure valves for your system, there are several factors to consider:
1. Pressure Rating
The valve’s pressure rating must match or exceed the operating pressure of your system. Choosing a valve that can handle the required pressure levels will prevent potential failures and improve system reliability.
2. Material Composition
The materials used in the valve’s construction must be compatible with the fluids or gases it will handle. Corrosion resistance, temperature tolerance, and durability are critical aspects to evaluate when selecting valve materials, especially in industries like chemical processing or power generation.
3. Flow Rate Requirements
Different valve types offer varying levels of flow control precision. Systems that require fine adjustments in flow will benefit from needle valves, while systems needing full, unobstructed flow may opt for gate valves.
4. Maintenance and Accessibility
Regular maintenance is essential for ensuring the longevity of high-pressure valves. Consider how accessible the valve is for inspection, repair, and replacement. A valve that is easy to maintain will save time and reduce downtime.
Conclusion
In high-pressure environments, selecting the right high pressure valve can make a significant difference in system performance, safety, and durability. Whether used in oil and gas, chemical processing, or power generation, these valves provide the control and reliability needed for successful operations.
Read Also
Download Free Piping PDF for Interview Preparation
Download Free Piping PDF for Interview Preparation
What is gasket and their types
What is a valve and its types? Â