Introduction to Deep Reactive Ion Etching:
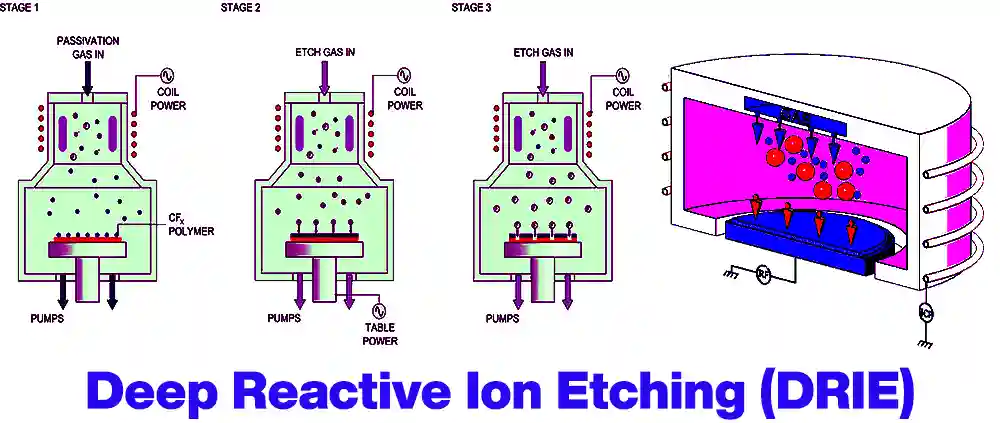
Deep Reactive Ion Etching: In the fields of microfabrication and semiconductor manufacturing, accuracy and efficiency are most important. One technique that has completely changed the fabrication of complex microstructures is Deep Reactive Ion Etching (DRIE). This advanced technology, also known as the Deep RIE or Bosch process, enables the precise etching of deep, high-aspect-ratio features in a variety of materials. In this article we will learn the principles, applications, and advantages of deep reactive ion etching, highlighting its importance in the semiconductor industry and beyond.
Understanding Deep Reactive Ion Etching
Deep reactive ion etching is an anisotropic etching process that involves the removal of material from a substrate using a combination of chemical and physical mechanisms. Unlike conventional isotropic etching, which etch uniformly in all directions, DRIE is highly directional and produces high-aspect-ratio structures with excellent depth control.
DRIE Process
Masking and Lithography: The first step in DRIE involves defining the pattern to be etched on the substrate. This is achieved through advanced photolithography techniques, where a mask is created with the desired pattern.
Plasma generation: Once the mask is in place, the substrate is placed in a vacuum chamber where a plasma composed of reactive gases such as SF6 and C4F8 is generated.
Ion acceleration and chemical reactions: The plasma contains charged ions which are accelerated towards the substrate, causing chemical reactions on the exposed surfaces. These reactions create volatile etching products that are removed from the surface.
Passivation and Etch Cycle: A key aspect of the DRIE process is the etch/passivation cycle. Reactive ions remove material during the etching phase, while the passivation phase deposits a protective layer on the sidewalls of the etched features. This cyclic process allows for a higher aspect ratio without significant side cropping.
Bosch Process: The Bosch process, a variant of DRIE, employs alternating etch/passivation cycles, resulting in improved sidewall smoothness and reduced sidewall scalloping.
Applications of deep reactive ion etching
Microelectromechanical Systems (MEMS): DRI plays an important role in the fabrication of MEMS devices, such as accelerometers, gyroscopes, and microfluidic devices. Its ability to create precise and deep features allows for the complex structures required in these applications.
Microelectronics: In semiconductor manufacturing, DRIE is used to create high-aspect-ratio features in integrated circuits, including through-silicon vies (TSVs) for 3D chip stacking and other specialized structures.
Photonic Devices: DRIE is engaged in manufacturing optical waveguides, micro-mirrors and other photonic devices to enable advanced optical communication systems.
Medical devices: The ability to create complex and precise structures makes DRIE valuable in the production of microfluidic devices, micro-needles and bio-sensing platforms for medical applications.
Advantages of Deep Reactive Ion Etching
High Aspect Ratio: DRIE excels at producing structures with high aspect ratios, allowing the creation of deep features at the micrometer scale.
Anisotropic Etching: Unlike isotropic etching, DRIE is anisotropic, resulting in vertical sidewalls and well-defined structures.
Scalability: DRIE is easily scalable to mass production, making it an ideal choice for high-volume microfabrication.
Selectivity: The process provides excellent selectivity, which enables the etching of specific materials while protecting others.
Conclusion
Deep reactive ion etching (DRIE) is at the forefront of microfabrication technology, enabling the fabrication of complex and high-aspect-ratio structures with unmatched precision. Its applications in MEMS, microelectronics, photonics, and medical devices have transformed various industries. As the semiconductor industry and related fields continue to grow, DRIE is bound to grow in importance, enabling the realization of smaller, smarter.
Watch out for videos related to oil and gas industry maintenance and shutdown
Read out PIPING : The Powerful Lifeline of the Oil & Gas Industry in 2023
Download Free PDF related to Piping Question Answer