Types of welding joints PDF Introduction
Butt welding is an important manufacturing process which is one of the most commonly used welding techniques, that involves joining of two pieces of metal in a seam-to-seam configuration along their edges. This method is widely used in various industries due to its simplicity, efficiency and ability to produce strong and durable joints. In this article, we’ll study about butt welding, exploring its principles, applications, advantages, and challenges.
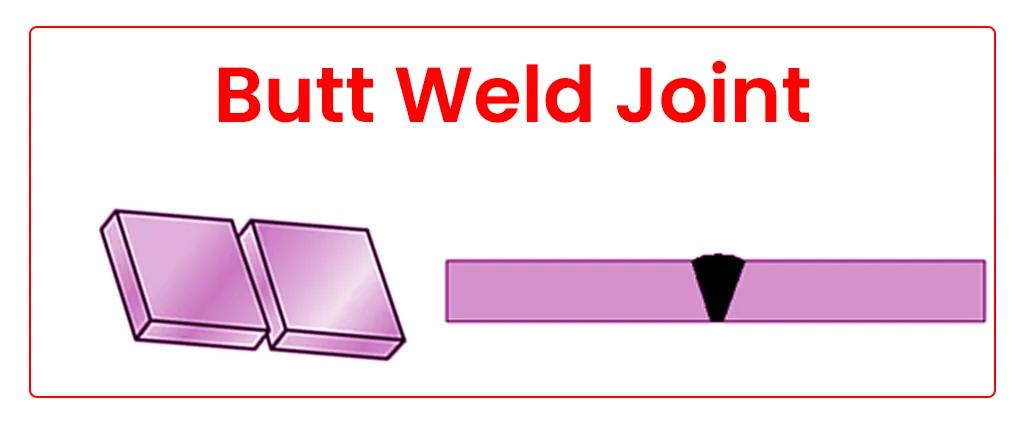
Understanding of Butt Welding
Butt welding is a fusion welding process that involves melting the edges of two metal workpieces to be joined and then fusing them together to form a single, continuous piece. The process typically involves the application of heat, which can be generated using a variety of sources such as electric arcs, gas flames, or laser beams. The heated metal edges are brought into contact and pressed together to form a tight joint to make a butt welding. As the metal cools and solidifies, the bond becomes strong and permanent.
Types of Butt Welding
There are several types of butt welding, each tailored to specific applications and needs. The most common types include:
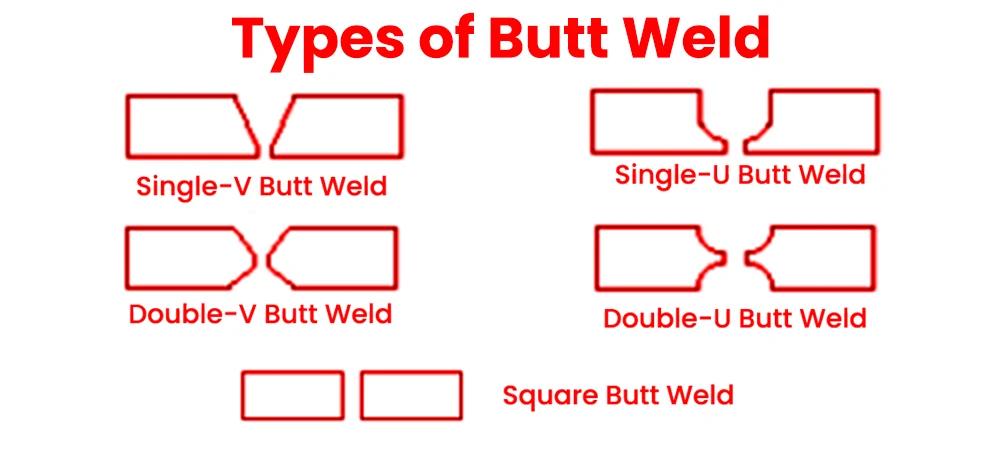
A. Single-V Butt Welding:
This type of weld is used for plates or sheets at least 1/8 inch thick. The edges of the workpiece are chamfered to form a “V” shape, and a welding electrode or filler material is added to the bottom of the “V” during the welding process.
B. Double-V Butt Welding:
This weld type involves beveling the edges of both workpieces facing each other to form two “V” shapes. It provides excellent penetration and is often used for thicker plates.
C. Single-U Butt Welding:
Similar to a single-V weld, but with a “U” shape instead. It is used for thin materials, and welding is done from one side.
D. Double-U Butt Welding:
Both edges are beveled into a “U” shape, similar to a double-V weld. It is used for thicker materials that require complete penetration.
E. Square Butt Welding:
The edges of the workpiece are squared without any beveling. It is used for thin materials and in cases where welding from both sides is not possible.
Applications of Butt Welding
Butt welding is widely used in many industries because of its versatility and ability to form strong, continuous joints. Some major applications include:
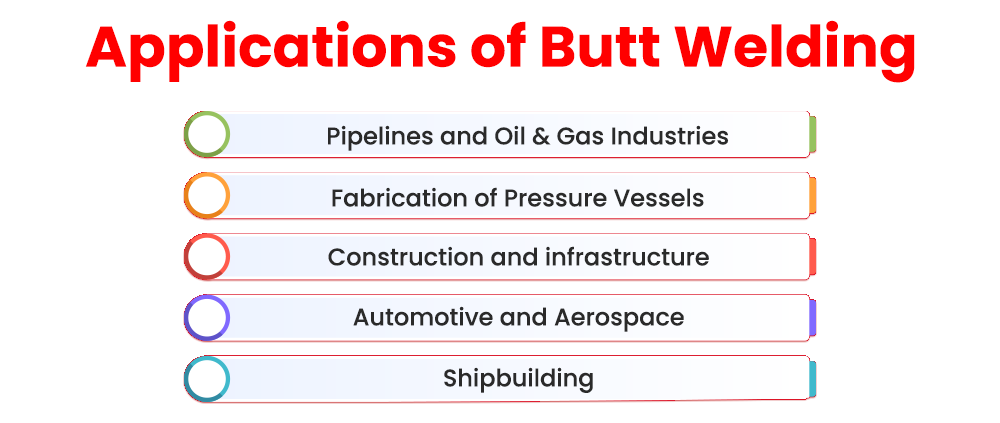
A. Butt welding used in construction and infrastructure:
In the construction sector, butt welding is used to join structural steel components used in buildings, bridges, and other infrastructure projects. This ensures the overall strength and integrity of the structures.
B. Butt welding used in pipelines and Oil & Gas Industries:
Butt welding is used extensively in the construction of pipelines for the transportation of oil, gas and other liquids. It provides leak resistant and durable joints that can withstand high pressure and harsh environmental conditions.
C. Butt welding used in Automotive and Aerospace:
The automotive and aerospace industries use butt welding to assemble a variety of metal components in vehicles, aircraft, and spacecraft. The joints made are important to ensure safety and performance.
D. Butt welding used in Shipbuilding:
Butt welding is a fundamental process in shipbuilding, used to join steel plates and create waterproof and strong structures.
E. Butt welding used in Fabrication of Pressure Vessels:
Pressure vessels used in various industrial processes are often assembled using butt welding due to its ability to produce high strength joints capable of withstanding internal pressures.
Advantages of Butt Welding
Butt welding offers several advantages that make it a preferred joining technique in a variety of applications:
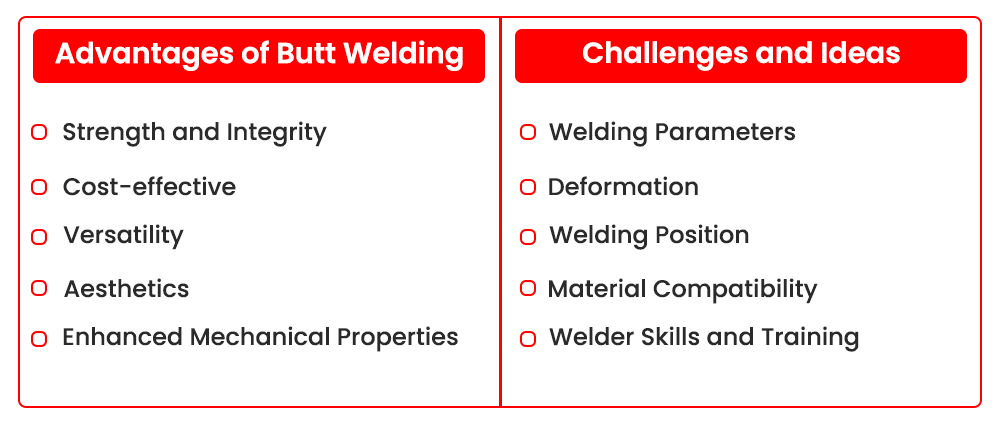
A. Butt welding Strength and Integrity:
Butt welds produce joints with excellent strength and structural integrity. The absence of additional materials (such as fasteners) ensures a consistent and uniform connection between the workpieces.
B. Butt welding Cost-effective:
Since butt welding does not require additional fasteners or connectors, it can be a cost-effective joining method in the long run.
C. Butt welding Versatility:
The variety of butt weld types allows for its application on a variety of materials, thicknesses, and configurations.
D. Butt welding Aesthetics:
Butt welding results in clean and smooth joints, which is desirable in many applications, especially where aesthetics matter.
E. Butt welding Enhanced Mechanical Properties:
Properly executed butt welds can maintain the mechanical properties of the base metal, ensuring that the joint can withstand the same loads and stresses.
Butt welding Challenges and Ideas
While butt welding is a valuable technology, it comes with some challenges and considerations that need to be addressed for successful implementation:
A. Welding Parameters:
Getting the right welding parameters, such as heat input, welding speed and electrode/filler material selection, is critical to obtaining a strong and defect-free weld.
B. Deformation:
During the welding process, heat can cause local expansion and contraction of the workpiece, which can lead to deformation. Proper fixing and temperature control are essential to minimize this effect.
C. Welding Position:
Welding in various positions (eg, flat, horizontal, vertical, overhead) can affect the quality and efficiency of butt welds. Some positions may require special techniques and equipment.
D. Material Compatibility:
Butt welding is best suited for similar or compatible metals. Adding different materials may require additional ideas and techniques.
E. Welder Skills and Training:
Skilled welders with the proper training and experience are essential to achieving consistently high quality butt welds.
Conclusion of Butt welding
Butt welding is a powerful and versatile joining technique that plays an important role in a variety of industries. Its ability to form strong, continuous joints makes it indispensable in applications where structural integrity and durability are paramount. From construction to aerospace, butt welding is shaping modern infrastructure and technology. As technology advances, we can expect more innovations in welding equipment, techniques, and materials that will propel butt welding to new heights of efficiency and excellence.\
Read Also
Download Free Piping PDF for Interview Preparation
nuts and bolts specification astm-a193-b7 and a194-2h
1 thought on “Butt Welding: Types of welding joints PDF”