Arc Welding Introduction
Arc welding is one of the most widely used and important welding processes in the manufacturing and construction industries. It is a versatile technique that allows metals to be joined using an electric arc to melt the workpiece and fuse them together. The purpose of this article is to provide a comprehensive guide to arc welding, including its history, types, working principle, equipment, safety measures, and applications.

History of Arc Welding
Arc welding has a rich history dating back to the 19th century when Sir Humphry Davy invented the electric arc in 1800. However, practical applications of arc welding were not developed until the late 1800s and early 1900s. The carbon arc welding process, invented by Nikolay Benardos and Stanisław Olszewski in the 1880s, was one of the first successful methods used for welding. In this technique a carbon electrode was used to create an arc between the electrode and the workpiece.
The introduction of metal arc welding in the early 20th century marked a significant advance in this field. CJ Pioneers such as Holslag and Oscar Kjellberg improved the process by using metal electrodes that were more efficient and provided better results. Subsequently, Shielded Metal Arc Welding (SMAW), also known as stick welding, emerged as the dominant arc welding method.
During the 20th century, several other arc welding processes were developed, including gas metal arc welding (GMAW), gas tungsten arc welding (GTAW), flux-cored arc welding (FCAW), and submerged arc welding (SAW). These advances revolutionized the welding industry, making arc welding more accessible, efficient, and versatile.
Types of Arc Welding
There are several types of arc welding processes, each with specific characteristics and applications:

A) Shielded Metal Arc Welding (SMAW)
SMAW, commonly known as stick welding, is a manual arc welding process. It uses a consumable electrode coated with flux to protect the weld pool from atmospheric contamination. SMAW is widely used in construction, repair and maintenance applications due to its portability and versatility.
B) Gas Metal Arc Welding (GMAW)
GMAW, also known as MIG (Metal Inert Gas) welding, uses a continuous solid wire electrode and a shielding gas, which may be inert (eg, argon) or active (eg, carbon dioxide). . It is widely used for welding of various metals and is known for its high productivity and ease of automation.
C) Gas Tungsten Arc Welding (GTAW)
GTAW, commonly known as TIG (Tungsten Inert Gas) welding, uses a non-consumable tungsten electrode to produce the weld. Depending on the application, a different filler metal may be used. GTAW is preferred for its accuracy and ability to weld thin materials, making it suitable for aerospace and artistic applications.
D) Flux-cored arc welding (FCAW)
FCAW is similar to GMAW but uses a tubular electrode filled with flux, thereby eliminating the need for an external shielding gas. It is commonly used in heavy welding applications and is suitable for outdoor or windy conditions.
E) Submerged Arc Welding (SAW)
SAW involves feeding a continuous, consumable bare wire electrode into the weld zone, which is submerged under a layer of granular flux. It is often used in high-speed, high-deposition welding of thick materials, such as in shipbuilding and structural fabrication.
Working Principle of Arc Welding
Arc welding works on the principle of creating an electric arc between the electrode and the workpiece. When electric current passes through the electrodes, it ionizes the surrounding air or shielding gas, creating a conductive plasma path. The intense heat generated by the arc melts both the electrode and the workpiece, forming a molten pool. As the pool cools, the molten metal solidifies and fuses the workpieces together, forming a strong joint.
The success of arc welding depends on maintaining a stable arc and controlling welding parameters such as current, voltage, travel speed and electrode composition. To obtain a consistent and defect-free weld, welders must create an arc and maintain the correct distance between the electrode and the workpiece.
Arc Welding Equipment
Arc welding requires specific equipment to suit the welding process chosen. Here are the components needed for common arc welding methods:
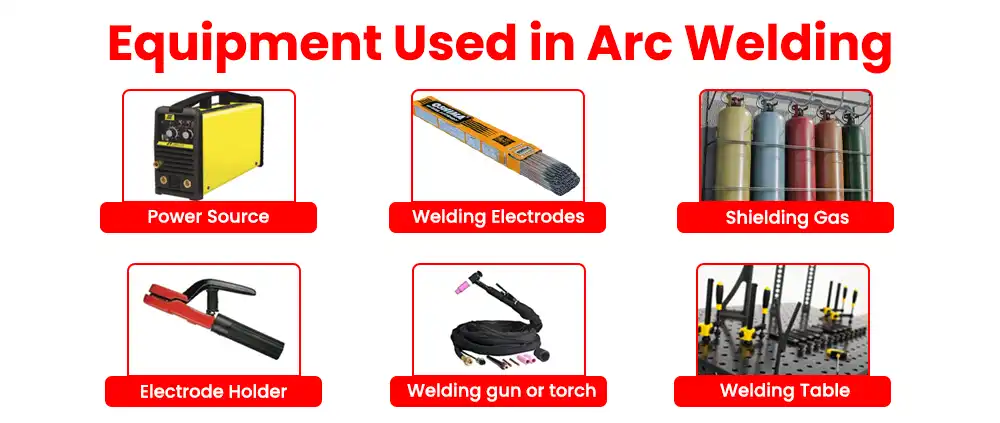
A) Power Source:
The power source provides the electric current required for arc welding. This can be an AC (Alternating Current) or DC (Direct Current) machine, depending on the welding process and requirements.
B) Electrodes:
Electrodes are the essential consumables used in arc welding. The type of electrode varies depending on the welding process and the metals being welded.
C) Shielding Gas:
In some arc welding methods, such as GMAW and GTAW, a shielding gas is used to protect the weld pool from atmospheric contamination.
D) Welding gun or torch:
The welding gun or torch holds the electrode and directs the arc towards the welding area.
E) Electrode Holder:
The electrode holder secures the electrode and allows the welder to maintain a safe distance from the arc.
F) Welding Table or Workpiece Clamp:
A stable welding surface or workpiece clamp is essential to ensure proper alignment and positioning during welding.
Safety Measures In Arc Welding
Arc welding poses a number of hazards, and proper safety measures are essential to protect the welder and others in the vicinity. Some key safety precautions include:
A) Personal Protective Equipment (PPE):
Welders should wear appropriate PPE, including a welding helmet with dark lenses, welding gloves, flame-resistant clothing, and safety glasses.
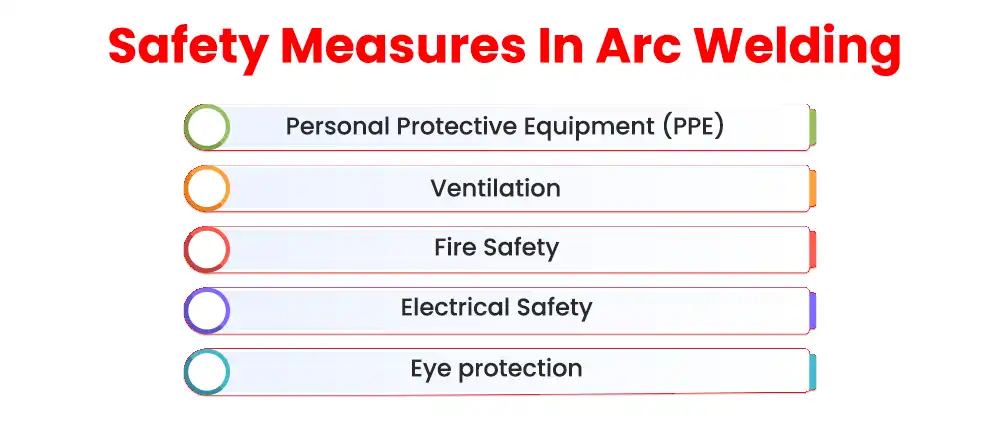
B) Ventilation:
Adequate ventilation is important to prevent accumulation of welding fumes and gases, which can be harmful if inhaled.
C) Fire Safety:
Arc welding produces intense heat, sparks and molten metal. Welders must have a fire extinguisher and must clear the area of flammable materials.
D) Electrical Safety:
Arc welding involves high voltages and currents. Insulated tools and equipment must be used, and proper grounding is essential to prevent electric shock.
E) Eye protection:
Welders must wear proper eye protection to protect their eyes from the intense light and harmful UV radiation generated during welding.
Applications of Arc Welding
Arc welding is used in a variety of industries because of its versatility and ability to join different metals. Some common applications include:
A) Construction and infrastructure:
Arc welding is used extensively in the construction of buildings, bridges and other infrastructure projects where high-strength joints are required.
B) Automotive and Transportation:
Welding is essential to the manufacturing of vehicle frames, bodies, and other components in the automotive industry.
C) Shipbuilding:
Arc welding is important in shipbuilding to create watertight joints and ensure the structural integrity of ships.
D) Aerospace:
The precision and cleanness of GTAW make it suitable for welding critical aerospace components.
E) Pipelines and Oil/Gas Industries:
Welding is used in the construction and maintenance of pipelines and various oil and gas industry components.
F) Art and Sculpture:
GTAW is often employed to create complex metal art and sculptures because of its precision and controllability.
Conclusion
In conclusion, arc welding is an important and versatile joining process. Its rich history, from the discovery of the electric arc by Sir Humphry Davy to the development of various arc welding techniques by pioneers, highlights its continued growth and importance in modern manufacturing.
Various types of arc welding processes including shielded metal arc welding (SMAW), gas metal arc welding (GMAW), gas tungsten arc welding (GTAW), flux-cored arc welding (FCAW), and submerged arc welding (SAW). Each method has its own strengths and limitations, making it essential for the welder to choose the process best suited for the specific tasks.
The working principles of arc welding, centered on creating and maintaining a stable electric arc, require skilled operators. The selection of appropriate equipment, such as power sources, electrodes, shielding gases and welding torches, is critical in ensuring efficient and effective welding operations.
Safety is of paramount importance in arc welding due to the hazards associated with intense heat, fumes, sparks and UV radiation. Welders must follow strict safety measures, wear appropriate personal protective equipment (PPE), and maintain a safe work environment to protect themselves and others.
Finally, arc welding remains an indispensable and ever-evolving technology that plays an important role in shaping the world we live in.
Read Also
Download Free Piping PDF for Interview Preparation
nuts and bolts specification astm-a193-b7 and a194-2h
1 thought on “Arc Welding: Types and Working Principle Download 5 Free PDF”