Introduction of Heat Exchanger
In the world of refining, heat exchangers play an important role in optimizing processes and improving energy efficiency. Heat Exchangers are important components that are used to transfer heat from one liquid to another without coming in direct contact with the liquid. This exchange of heat is necessary for various refining operations, including distillation, cracking, reforming, and other processes aimed at turning crude oil into valuable final products. In this article, we will discuss the importance of heat exchangers in refineries and explore some of the common types used in these complex industrial facilities.
Importance of Heat Exchangers in Refineries
Refineries are huge plants where crude oil is processed and converted into a wide range of products such as gasoline, diesel, jet fuel and various petrochemicals. During this complex refining process, a large amount of heat is generated and needs to be managed efficiently to ensure smooth operation, safety and cost-effectiveness with the help of heat exchanger.
Heat exchangers play an important role in the following aspects of refinery operations:
Energy Conservation
Refineries are energy-intensive facilities, and effective heat exchange enables them to recover and reuse the heat generated during various processes. This energy conservation reduces overall fuel consumption and operating costs with the help of heat exchangers.
Temperature control
Heat exchangers help control the temperature of process streams, ensuring that reactions occur at desired rates and preventing damage to equipment due to excessive temperatures.
Condensation and Evaporation
During the refining process, some components of the crude oil need to be condensed or vaporized. Heat exchangers facilitate these phase changes by transferring heat between the fluids involved.
Heat Recovery
Many refining processes generate hot by-products or waste streams. Heat exchangers can recover heat from these streams and reuse it for other parts of the refinery, reducing waste and improving energy efficiency.
Safety and environmental benefits
Efficient heat exchangers help maintain stable operating conditions, reducing the risk of equipment failure and potential environmental hazards.
Types of Heat Exchangers Used in Refineries
A variety of heat exchangers are employed in refineries, each tailored to specific applications and operational requirements. Some common types include:
Shell and Tube Heat Exchangers
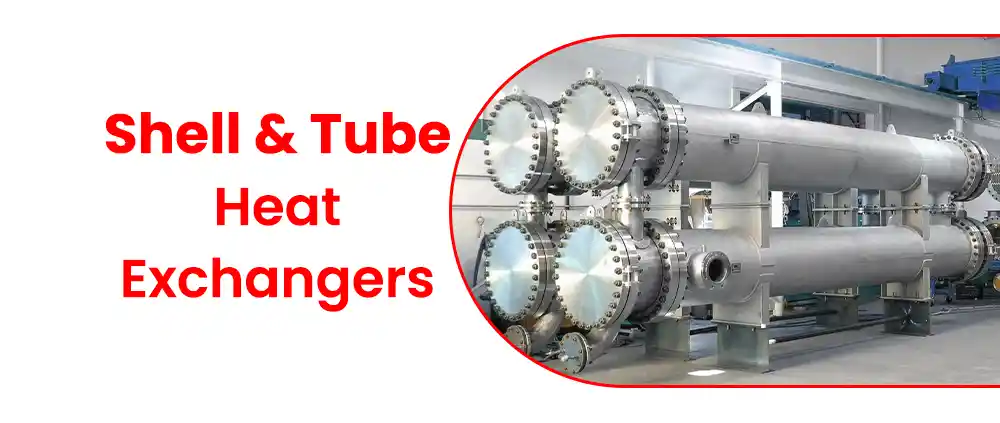
Shell and tube heat exchangers are the most widely used type in refineries due to their versatility and effectiveness. They consist of a bundle of tubes (inner vessels) enclosed within a shell (outer vessel). One fluid flows through the tubes, while the other flows around the outside of the tubes in the shell. Heat is transferred between the fluid inside the tubes and the fluid in the surrounding casing. These exchangers are suitable for high pressure and high temperature applications. Based on their construction and design, there are several types of shell and tube heat exchangers.
Main types of Shell and Tube Heat Exchanger include:-
Fixed Tube Sheet Heat Exchanger
In this type, the tubes are fixed in a tube sheet, which is welded to the shell. This design is simple and cost effective but may have limitations in terms of thermal expansion.
U-tube heat exchanger
This design features U-shaped tubes, which allow for differential thermal expansion between the shell and the tubes. It is suitable for applications where there is a need to separate one fluid from another.
Floating Head Heat Exchanger
In this type, one end of the tubes is attached to the tube sheet while the other end is free to move within the shell. This design allows easy maintenance and cleaning of the tubes.
Fixed tube-sheet with expansion joint
This type is similar to the fixed tube sheet heat exchanger, but includes an expansion joint to accommodate thermal expansion and contraction.
Kettle reboiler
This is a specific type of shell and tube heat exchanger used as a reboiler in distillation columns. The tubes are immersed in the liquid, and heat is provided to generate vapor for the distillation process.
Plate Heat Exchangers

In plate heat exchangers a number of plates are placed together to form alternating channels for the two fluids. They are compact and ideal for applications where space is limited. Plate heat exchangers are typically used for low-viscosity fluids and in situations where frequent cleaning is required.
Air-cooled Fin-Fan heat exchangers (AFC)

In cases where water is scarce or not suitable for cooling, AFCs come in handy. These type of heat exchangers use ambient air to cool the process fluids. They are especially valuable in areas with a warm climate.
Finned Tube Heat Exchangers

Finned tube heat exchangers increase the heat transfer surface area, thereby increasing heat exchange efficiency. They are often used in air-cooling applications for better heat dissipation.
Double pipe heat exchangers
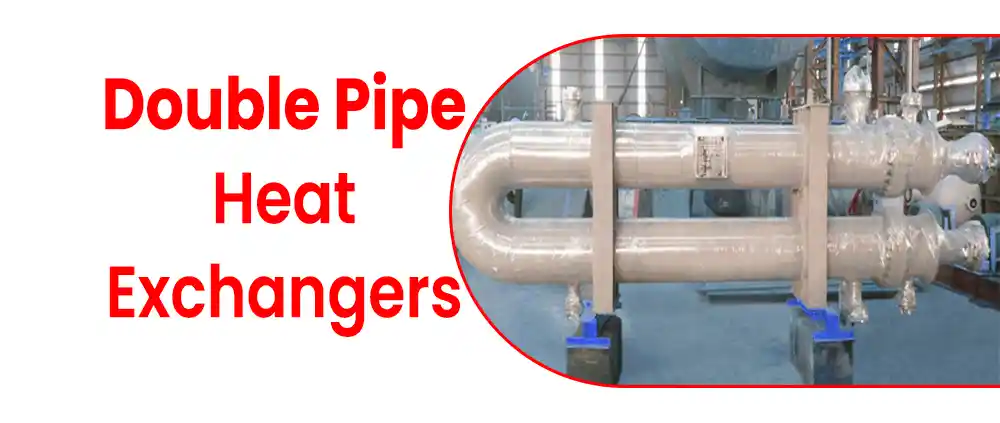
Double pipe heat exchangers are simple and cost effective, consisting of two concentric pipes where one fluid flows through the inner pipe while the other flows through the annular space. These are generally used for low to medium heat transfer requirements.
Plate-fin heat exchangers

Plate-fin heat exchangers are compact and lightweight, making them suitable for applications where space is limited. They are commonly used in cryogenic processes, such as liquefied natural gas (LNG) production.
Spiral Heat Exchanger

A spiral heat exchanger is made by rolling two long metal plates around a center core to form two concentric spiral flow paths, one for each fluid. The edges of the plate are welded shut so that each fluid remains within its own passageway and no flows bypass or mix.
Conclusion
Heat exchangers are indispensable components in refinery operations, enabling efficient heat management, energy conservation and temperature control. The different types of heat exchangers used in refineries meet different operational requirements and play a vital role in increasing the overall efficiency and safety of these complex industrial facilities. As refineries continue to evolve and focus on sustainable practices, heat exchangers will continue to be an important technology in the quest for optimum performance and reduced environmental impact.
Read Also
Download Free Piping PDF for Interview Preparation
1 thought on “Heat exchangers used in oil and gas industries and their types Download 5 Free PDF”