Introduction
A demister pad is a device that removes small liquid droplets from a gas stream. It is similar to an air filter, but it is more efficient at removing smaller particles. Demister pads are commonly used in process piping applications to protect downstream equipment from fluid ingress, which can cause rust, corrosion, and other problems.
History of demister pad
In the late 1950s, foreigners developed a device made of special wrinkled woven mesh to remove small liquid foam inclusions from gas. It was found to be very efficient and with low resistance, unmatched by other gas-liquid separation equipment. As a result, it was widely accepted and used in a wide range of applications.
Demister pads are typically placed on top of packing towers to ensure mass transfer efficiency and reduce board spacing. They are widely used in vertical cylindrical vapor-liquid separation equipment in the chemical, petroleum, pharmaceutical, light industry, and metallurgy industries. Demister pads can also be used in desulfurization and other production processes to remove oil mist, poisonous, and toxic gases.
Working principle of demister pad
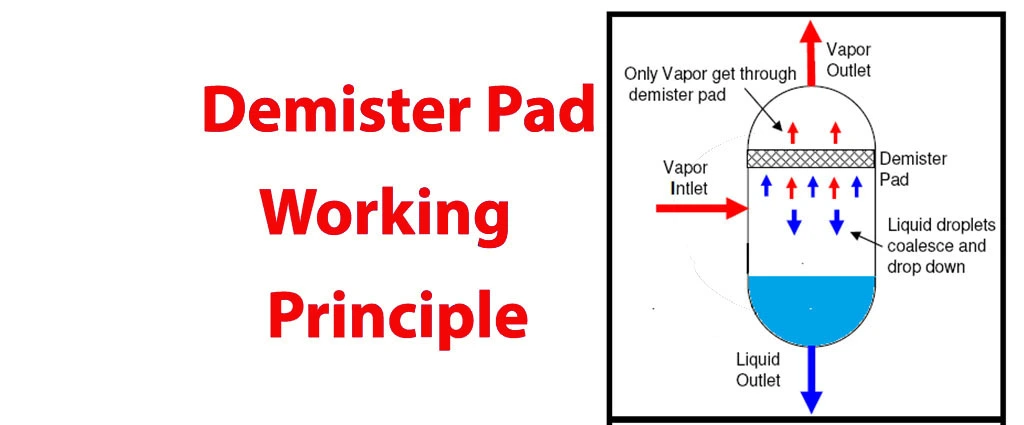
When a gas containing mist rises at a constant speed and passes through the wire mesh of a demister pad, the inertia of the rising mist causes it to collide with and adhere to the mesh filaments. The mist then spreads over the surface of the filaments and the droplets move along the filaments until they reach the intersection of two wires. At this point, the droplets grow larger and separate from the filaments.
The separation of the gas into droplets improves operating conditions, optimizes process indicators, reduces equipment corrosion, extends equipment life, increases the processing and recovery of valuable materials, protects the environment, and reduces air pollution.
How does a demister pad look like
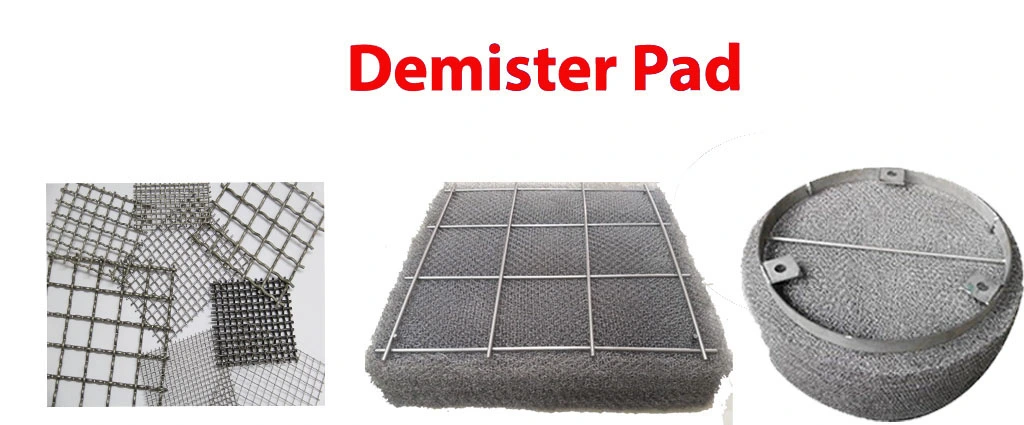
Flooding was the main factor considered when selecting a demister for the issue described here. In a typical demister installation, a thin layer of bubbling liquid (1 or 2 inches in height) forms at the bottom of the demister pad. This is known as the dissolution zone. The remaining area above the liquid layer, known as the active zone, captures the droplets.
Liquid droplets collect on the wire mesh and then drain by gravity into the dissolution zone. Eventually, the droplets drip into the liquid pool at the bottom of the vessel. As the velocity or liquid loading increases, the height of the dissolution zone increases and advances into the active zone. When the dissolution zone reaches the active zone, flooding occurs and liquid is carried over into the downstream piping and equipment.
How Demister Pads Work
Demister pads are made of woven wire mesh with a large surface area. When a gas stream containing liquid droplets passes through a demister pad, the droplets collide with the mesh and coalesce, or combine, to form larger droplets. These larger droplets are too heavy to be carried along with the gas stream, so they fall out and collect at the bottom of the demister pad.
Advantages of Demister Pads
Demister pads have a number of advantages over other methods of removing liquid entrainment from gas streams, including:
- High efficiency at removing small liquid droplets
- Low pressure drop
- Small footprint
- Easy installation and maintenance
Applications of Demister Pads
Demister pads are used in a wide variety of process piping applications, including:
- Distillation towers
- Fractionating columns
- Scrubbers
- Knock-out pots
- Vapor separators
- Compressor intakes
- Turbine intakes
Conclusion
Demister pads are a highly effective and efficient way to remove liquid droplets from gas streams. They are commonly used in process piping applications to protect downstream equipment from fluid ingress.
Demister pads work by aggregating small liquid droplets into larger droplets that are too heavy to be carried with the gas stream. They have several advantages over other methods of removing liquid droplets, including high efficiency, low pressure drop, small footprint, and easy installation and maintenance.
Demister pads are commonly used in process piping applications such as distillation towers, fractionating columns, scrubbers, knock-out pots, vapor separators, compressor intakes, and turbine intakes.
Read Also
Mechanical maintenance engineer roles and responsibilities
What are the internals in distillation column
What are the internals of a distillation column?
Types of Work Permit | Hot Work Permit | Cold Work Permit